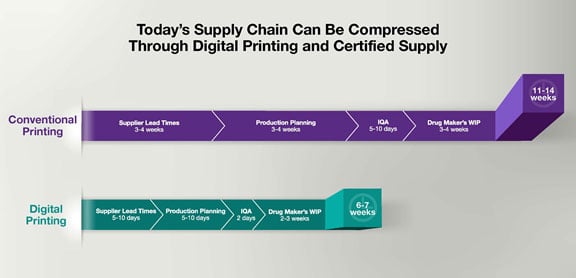
As you begin the process of determining whether or not to transition some or all of your packaging to Digital Printing, keep in mind the principal benefits of the technology:
- Has the potential to shrink your packaging workflow from 17 steps to just 3 steps. In the past, conventional printing took 17 steps, from art generation to plate making to printing. That meant 17 opportunities for errors, defects, and waste. The advent of computer-to-plate technology (CTP) eliminated many of these manual steps but the cost of excessive make-ready, a higher internal cost of quality (defects), and the use of plates still required longer runs to achieve the lowest price. The advent of digital offset print production has shrunk the process to 3 steps, as print production is fully digital and highly compressed.
- Can greatly enhance the value proposition. This is based on the savings and benefits of not having any obsolete inventory, shrinking time-to-market, faster order turnaround time, dramatic shrinking of cycle times, and eliminating several steps between proofs/concepts and prototypes. Digital Printing also saves on the cost of prepress and the per-thousand cost on labels or cartons. Healthcare end users report saving an average of $400 per item on plates, and an on-time delivery of 98.5%.
- Enhances supply chain efficiencies. With a compressed supply chain, you will experience the following:
- A shorter timeline between FDA approval and arrival of packaging for new drugs and devices
- A faster transition to production
- Simplified customization of label designs to better target smaller markets, protect brands and implement track-and-trace solutions
- Cost-effective launching of a brand or expansion into new markets for low-volume SKUs
- Speed to test market for new designs
- Simplifies variable data on packaging. Digital Printing, whether on labels or cartons, makes it easy to print in-line variable data, in several forms. It supports development of an electronic pedigree and track-and-trace capability via serialization of each label or folding carton, using a unique numeric or alphanumeric code, one- or two-dimensional bar code, or radio frequency identification (RFID) tag.
- Digital is more environmentally friendly than conventional printing. First, make-ready is significantly reduced since Digital Printing enables “good labels” within a few minutes. This reduces wasted ink, materials, and support processes. In some cases users have found that digital production uses 4x less ink than conventional processes. And, since no printing plates are used, further waste and cost is avoided. HP Indigo ElectroInk products do not contain any substance listed under California Proposition 65, are recyclable, meet requirements of other global and regional initiatives, and produce no hazardous air pollutants. Digital Inks are mineral oil based and approved for indirect food contact.
